Unlocking the Potential of Pressure Die Casting Components
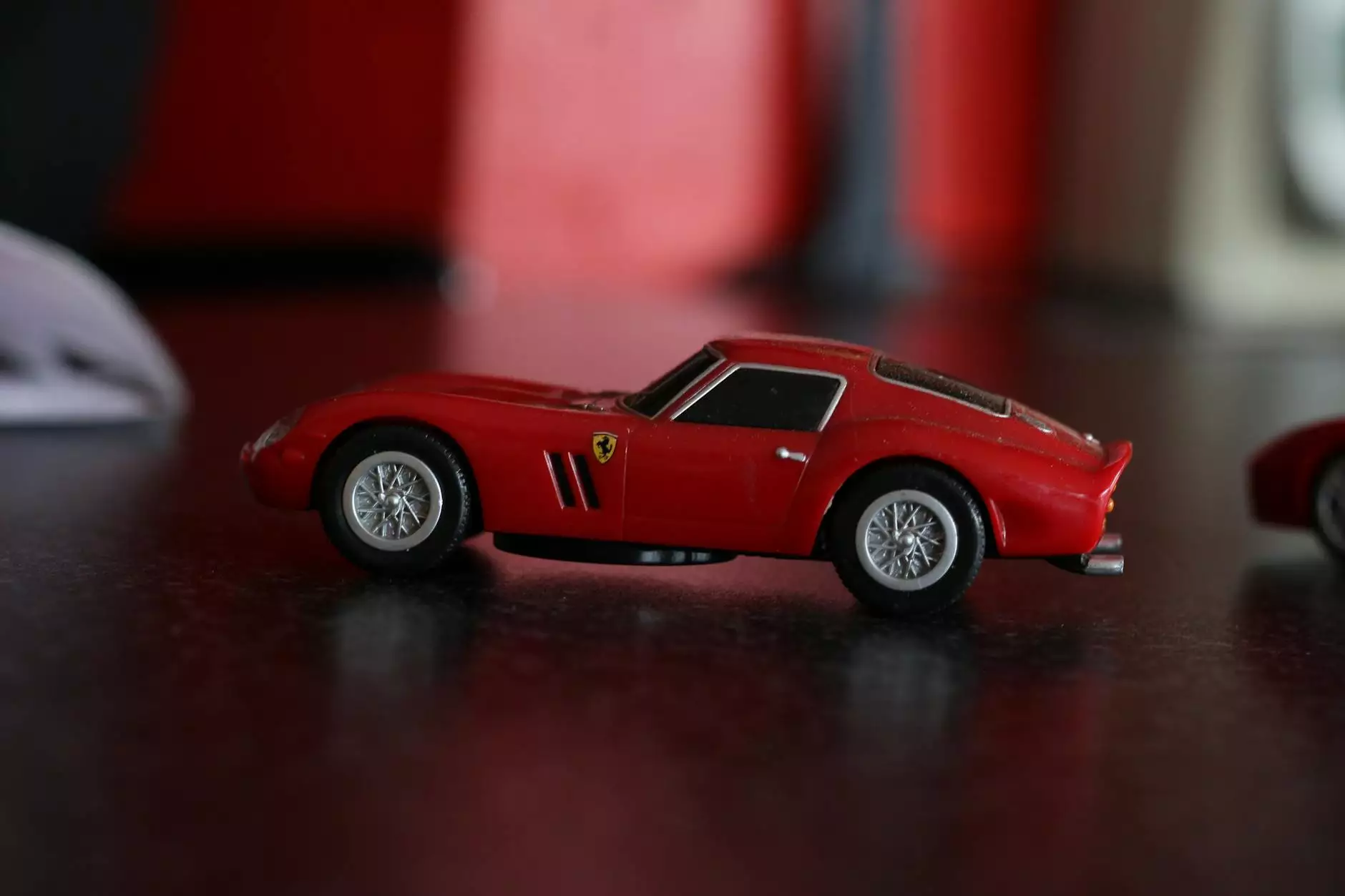
Pressure die casting has become an indispensable part of various manufacturing processes, offering exceptional precision, durability, and efficiency in the production of metal components. In this article, we will explore the intricacies of pressure die casting components, their benefits, applications, and how they hold a competitive edge in the realm of metal fabrication. This comprehensive guide aims to provide insights that will not only enhance your understanding but also assist you in making informed decisions for your business needs.
What is Pressure Die Casting?
Pressure die casting is a sophisticated manufacturing technique used to produce detailed metal components with high dimensional accuracy. It involves injecting molten metal into a mold at high pressure, ensuring that every intricate detail of the mold is captured in the final product. This method is widely utilized for producing parts made from non-ferrous metals like aluminum, zinc, and magnesium.
The Advantages of Pressure Die Casting Components
Understanding the advantages is crucial for businesses considering the transition to pressure die casting components. Here are the primary benefits:
- High Precision: The pressure-driven process allows for incredibly tight tolerances, reducing the need for extensive machining post-production.
- Scalability: Once the mold is made, it is easy to reproduce thousands of parts with minimal variability.
- Surface Finish: Pressure die casting components typically have a superior surface finish, which means they often require less post-processing.
- Material Efficiency: The process minimizes waste and maximizes yield, making it an environmentally friendly option.
- Rapid Production: The usage of molds ensures that components can be produced quickly, thus enhancing productivity.
The Pressure Die Casting Process Explained
The elaboration of the pressure die casting process is essential for grasping its capabilities. Here’s a breakdown:
- Die Preparation: The first step involves preparing the die, which consists of two halves and is usually made of tool steel.
- Melting the Alloy: The metal alloy is melted in a furnace and transferred to the injection system.
- Injection: Molten metal is injected into the die at high pressure, filling up the cavity quickly.
- Cooling: The molten metal is left in the mold to cool and solidify, which usually takes a few seconds.
- Die Opening: Once cooled, the die halves are separated to release the cast component.
- Trimming: Any excess material is trimmed off, and the final adjustments are made.
Applications of Pressure Die Casting Components
The versatility of pressure die casting components allows them to be used across numerous industries:
1. Automotive Industry
The automotive sector relies heavily on pressure die casting components for producing engine blocks, transmission cases, and various decorative elements. The lightweight nature of such components contributes to fuel efficiency without compromising safety.
2. Aerospace Applications
In aerospace, components such as brackets, housings, and torque tubes must meet stringent quality standards. Pressure die casting provides the necessary strength-to-weight ratio needed in flight applications.
3. Electronics Manufacturing
Electronic equipment often requires intricate housings and heat sinks that are best achieved through pressure die casting techniques. This process allows for precise fits and finishes that are critical in electronics design.
4. Consumer Products
Many everyday consumer products—from kitchen appliances to lighting fixtures—utilize die cast components, enhancing functionality and aesthetic appeal.
Challenges in Pressure Die Casting
While there are numerous advantages to using pressure die casting components, it is essential to acknowledge potential challenges:
- Tooling Costs: The initial investment in die tooling can be substantial, which may deter smaller businesses.
- Material Limitations: The process is predominantly suitable for non-ferrous metals, limiting options in some applications.
- Lead Times: Dependency on custom tooling can lead to longer lead times compared to other manufacturing methods.
Choosing a Reputable Manufacturer: DeepMould.net
Finding a reliable manufacturing partner is vital for ensuring the success of your project. DeepMould.net specializes in producing high-quality pressure die casting components, and here's why you should consider them:
- Expertise: DeepMould.net has years of experience in the industry, bringing a wealth of knowledge to each project.
- State-of-the-art Technology: Utilize the latest technology in die casting to ensure precision and efficiency.
- Customization: Their team works closely with clients to tailor solutions specific to project needs.
- Quality Assurance: Stringent quality control measures ensure that every component meets and exceeds industry standards.
The Future of Pressure Die Casting Components
As we look ahead, the future of pressure die casting components appears bright. Innovations in materials and processes continue to enhance the capabilities of die casting, making it an even more attractive option for manufacturers seeking efficiency and quality. The rise of 3D printing technologies may also shift the landscape, prompting advances in mold design and production speed.
Conclusion
In summary, pressure die casting components are crucial in enhancing the production efficiency and quality of a myriad of applications across various industries. By partnering with reputable manufacturers like DeepMould.net, businesses can leverage the inherent advantages of this technique to produce superior products that stand the test of time. With ongoing advancements in technology and methodology, the potential for pressure die casting continues to expand, making it a foundational component in the future of metal fabrication.
For more information on how pressure die casting components can benefit your business, visit DeepMould.net.