Understanding Plastic Molding for Electrical Applications
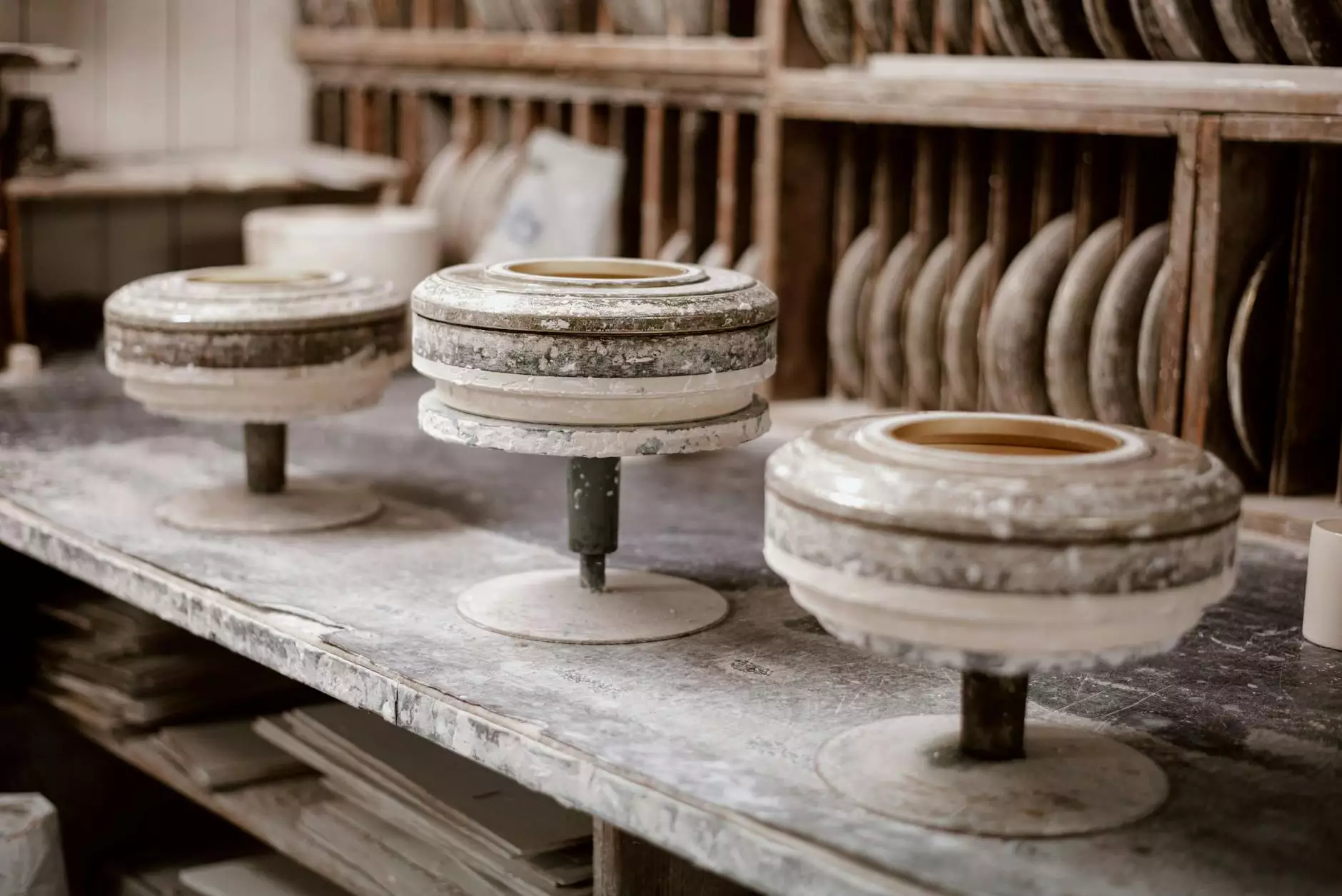
Plastic molding for electrical applications is increasingly becoming a cornerstone in the production of electrical components, enhancing both performance and reliability. This article delves into the intricacies of plastic molding, its types, benefits, and how it plays a vital role in the electrical industry.
The Basics of Plastic Molding
Plastic molding is a manufacturing process used to create parts by injecting molten plastic into a mold. This method allows for the creation of complex shapes and designs with high precision and efficiency. In the context of electrical applications, this process is pivotal for producing components like housings, connectors, and insulators.
Types of Plastic Molding
There are several types of plastic molding techniques employed in the electrical industry, each with unique advantages:
- Injection Molding: This is the most common method, where plastic is injected into a mold under high pressure. It is ideal for mass production.
- Blow Molding: Used primarily for creating hollow parts, this method involves inflating plastic into a mold, suitable for making items like containers.
- Rotational Molding: In this technique, plastic is heated and rotated in the mold, allowing it to coat the interior. It’s often used for larger parts.
- Thermoforming: Here, plastic sheets are heated and formed over a mold. This method is often used for simpler shapes.
Benefits of Using Plastic Molding in Electrical Applications
The adoption of plastic molding for electrical components offers numerous benefits that are essential for modern manufacturing:
1. Durability and Resistance
Modern plastics used in molding are engineered for high durability and can resist various environmental factors, including moisture, chemicals, and temperature fluctuations. This makes them ideal for electrical applications where reliability is paramount.
2. Lightweight Solutions
Compared to traditional materials like metals, plastic components are significantly lighter. This reduction in weight can lead to savings in shipping costs and easier handling during installation, becoming beneficial in large-scale electrical assemblies.
3. Cost-Effectiveness
Plastic molding is a cost-effective method for mass production. The ability to produce large quantities of items with minimal waste helps in reducing overall production costs, thus making it a preferred choice for manufacturing electrical components.
4. Design Flexibility
Plastic molding allows for incredible design flexibility. Complex shapes and intricate designs can be easily accomplished, enabling manufacturers to create tailored solutions for niche electrical applications.
5. Enhanced Safety
Many modern plastics used in plastic molding for electrical applications are non-conductive and can reduce the risk of electrical hazards. This enhances the safety of devices and systems that incorporate these components.
Applications of Plastic Molding in the Electrical Industry
Plastic molding is utilized in a wide range of electrical applications, showcasing its versatility:
- Electrical Enclosures: Protecting sensitive components from environmental damage.
- Connectors: Various connectors are produced using plastic molding, ensuring secure electrical connections.
- Insulators: Essential in preventing electrical flow where it's not intended, ensuring safety and performance.
- Switches and Dials: Created with precision for user-friendly operation.
The Process of Plastic Molding for Electrical Components
The process of plastic molding for electrical components typically follows these steps:
1. Design and Prototyping
Before any molding begins, a detailed design of the electrical component is created. This might involve CAD software to visualize and test the design.
2. Mold Creation
A mold is then crafted, often from steel or aluminum, depending on the production scale and intricacies of the part. This mold defines the final shape and features of the component.
3. Injection of Plastic
Once the mold is prepared, plastic pellets are heated until molten and injected into the mold. The pressure and temperature need to be precisely controlled to ensure quality.
4. Cooling and Finishing
After injection, the mold is cooled, allowing the plastic to harden. The part is then ejected from the mold, where finishing touches may be applied, such as trimming and surface treatment.
Quality Control in Plastic Molding for Electrical Components
Quality control is an indispensable part of the plastic molding for electrical applications process. It ensures that every component meets the necessary safety and performance standards:
- Material Verification: Ensuring that only high-quality materials are used in production.
- Dimensional Accuracy: Each part is measured for dimensional compliance against the specifications.
- Functional Testing: Components undergo testing to verify that they perform as expected under real-world conditions.
- Regulatory Compliance: Meeting industry standards relevant to electrical components.
The Future of Plastic Molding in Electrical Applications
As technology advances, the world of plastic molding for electrical applications is set to evolve further. Innovations such as 3D printing and sustainable materials are paving the way for new manufacturing processes that improve efficiency and reduce environmental impact.
Moreover, the integration of smart technology into electrical components calls for higher precision and functionality in design. Plastic molding will continue to play a crucial role in accommodating these sophisticated requirements, enabling manufacturers to create enhanced, intelligent products.
Choosing the Right Plastic Molding Partner
When considering plastic molding for electrical components, selecting a proficient manufacturing partner is essential. Look for a provider that has:
- Experience in the Industry: A partner with extensive knowledge of electrical components can ensure best practices.
- Advanced Technology: Access to modern machinery and techniques can improve the quality of production.
- Strong Quality Control Measures: A robust tracking and validation system is crucial.
- Custom Solutions: The ability to tailor solutions to meet specific project requirements is vital.
Summary
In summary, plastic molding for electrical applications is an essential manufacturing process that combines efficiency, quality, and adaptability. As the electrical industry continues to innovate, so too will the methods and materials involved in plastic molding, ensuring that it remains at the forefront of technological advancement. Selecting the right manufacturing partner can unlock the potential for developing top-tier electrical components that meet the growing demands of the industry.
For more information on our plastic molding services and how we can assist in your electrical component needs, visit deepmould.net.